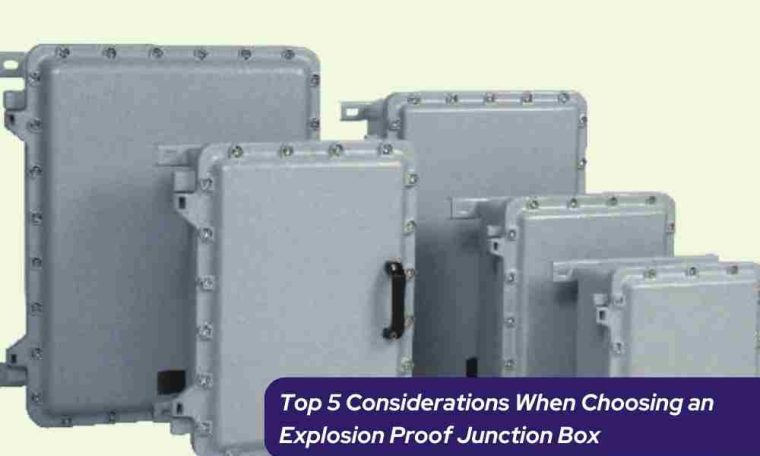
Introduction
In the world of industrial safety, one often-overlooked hero is the explosion-proof junction box. Getting the right one is crucial for keeping both people and equipment safe in risky environments. This guide breaks down the process into easy steps, making it a breeze for everyone to understand and pick the perfect explosion-proof junction box for their needs.
What’s the Deal with Explosion-Proof Junction Boxes?
What’s this Box All About?
An explosion-proof junction box is a special container designed to keep electrical sparks contained, preventing them from igniting any flammable gases or vapors nearby. It’s like a safety bubble for industries where explosive atmospheres might be hanging around.
Why Should You Care?
These boxes play a vital role. In places with combustible stuff, a little spark from a wonky wire could lead to a massive explosion. These boxes are built to trap any potential blasts, ensuring people stay safe, and equipment stays intact.
The Big 5 Things to Think About
Money Talks – Budgeting for Safety
1. Finding the Sweet Spot
Sure, safety is vital, but your wallet matters too. Check out different options, see what they offer, and weigh them against your budget.
2. It’s an Investment
See buying the box as a long-term thing. Quality might mean a bit more cash upfront, but it pays off in the long run with a box that lasts, does its job, and keeps everyone safe.
Dotting the I’s and Crossing the T’s – Certifications and Standards
When selecting an explosion-proof junction box for industrial applications, ensuring compliance with certifications and standards is crucial. This step adds an extra layer of assurance that the chosen equipment meets rigorous safety criteria. Let’s delve into the importance of these certifications and standards and understand the significance of each.
1. Play by the Rules
Certifications and standards are like the rulebook for explosion-proof junction boxes. They establish the criteria and tests that a product must pass to be considered safe for use in hazardous environments. Ignoring these standards is akin to playing with fire – quite literally.
Common Certifications
- ATEX Certification: Ensures compliance with European Union standards for equipment intended for use in explosive atmospheres.
- IECEx Certification: An international standard verifying conformity to explosion protection requirements.
- UL Certification: Issued by Underwriters Laboratories, it signifies that the product has undergone thorough testing to meet safety standards.
2. Ensuring Compliance with Industry Standards
Different industries may have specific standards that govern the use of explosion-proof equipment. Checking for compliance with these industry-specific standards ensures that the junction box is suitable for the intended application.
Industry-Specific Standards
- Oil and Gas Industry: API (American Petroleum Institute) standards might apply.
- Chemical Industry: ISO (International Organization for Standardization) standards relevant to chemical processes are crucial.
- Mining Industry: MSHA (Mine Safety and Health Administration) standards are essential for mining applications.
3. Markings Matter
Certified explosion-proof junction boxes bear specific markings indicating compliance with safety standards. Understanding these markings is key to recognizing a product’s adherence to regulations.
Also read – The Ultimate Guide to Selecting the Right Explosion-Proof Junction Box
Wrapping it Up
Picking the right explosion-proof junction box isn’t rocket science. By understanding the basics, thinking about the essentials, splurging where it matters, and making sure the box follows the rules, you can confidently choose a safety sidekick that’ll have your back in risky environments. In the world of hazardous zones, the right choice isn’t just a good idea – it’s a safety necessity.
Note: Also read our next blog: Ideal Holiday Home Companies in Dubai: Complete Checklist