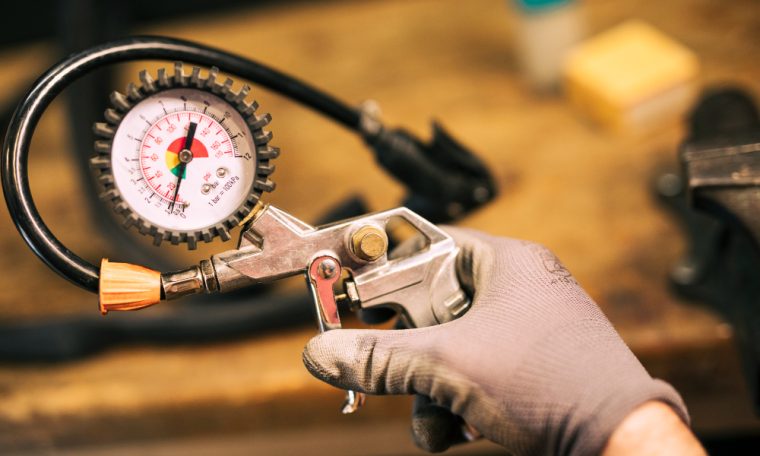
In today’s industrial landscape, helium leak testing system play a crucial role in ensuring the integrity and reliability of various products and components. These systems are widely used across industries such as automotive, aerospace, pharmaceuticals, and electronics to detect and locate leaks in sealed components and systems.
Understanding Helium Leak Testing
Helium leak testing is a highly sensitive method used to detect and quantify leaks in pressurized systems or components. The process involves pressurizing the test object with helium leak testing gas and then using a sensitive detector to measure any helium that escapes through leaks. Since helium is a small molecule that can penetrate even the tiniest of openings, it serves as an excellent tracer gas for leak detection purposes.
Key Components of a Helium Leak Testing System
A typical helium leak testing system consists of several key components, including:
- Helium Source: Provides a controlled supply of helium gas for pressurizing the test object.
- Test Chamber: Encloses the test object and allows for pressurization with helium gas.
- Vacuum Pump: Evacuates air from the test chamber to create a low-pressure environment for leak detection.
- Helium Detector: Sensitive instrument capable of detecting and quantifying helium gas concentrations.
- Data Acquisition System: Records and analyzes the results of the leak test for evaluation and documentation.
Factors Affecting Testing Effectiveness
Several factors can influence the effectiveness and accuracy of helium leak testing, including:
Leak Rate
The leak rate defines the quantity of gas that escapes through a leak per unit of time and is typically measured in units such as millibar liters per second (mbar∙L/s). Lower leak rates require more sensitive detection equipment and may necessitate longer test times to achieve reliable results.
Test Pressure
The test pressure refers to the pressure at which the test object is pressurized with helium gas during the leak test. Higher test pressures can increase the likelihood of detecting leaks but may also pose safety concerns and require specialized equipment.
Sensitivity of Detection Equipment
The sensitivity of the helium detector plays a critical role in detecting leaks accurately. Modern detectors with advanced features such as mass spectrometry or sniffer probes offer enhanced sensitivity and detection capabilities, allowing for the detection of smaller leaks with greater precision.
Testing Environment
The testing environment, including factors such as temperature, humidity, and background gas levels, can impact the accuracy and reliability of helium leak testing results. Controlling environmental variables and ensuring proper calibration of equipment are essential for obtaining accurate test results.
Benefits of Helium Leak Testing
Helium leak testing offers several advantages over other leak detection methods, including:
- High Sensitivity: Helium is an inert, non-toxic gas with excellent penetration capabilities, making it highly effective for detecting leaks, even in complex or hard-to-reach areas.
- Quantitative Results: Helium leak testing provides quantitative data on leak rates, allowing for precise evaluation and comparison of leak tightness.
- Non-Destructive: Unlike some other leak testing methods that may damage or alter the test object, helium leak testing is non-destructive, preserving the integrity of the component or system being tested.
- Versatility: Helium leak testing can be adapted to a wide range of applications and industries, making it a versatile and widely applicable method for leak detection.
Advanced Techniques and Best Practices
To further enhance the effectiveness of your helium leak testing system, consider implementing advanced techniques and best practices:
Automated Testing Solutions
Investing in automated helium leak testing solutions can streamline the testing process, improve efficiency, and reduce human error. Automated systems offer precise control over test parameters, consistent testing conditions, and real-time data monitoring, leading to faster turnaround times and enhanced reliability.
Integration with Production Processes
Integrating helium leak testing seamlessly into your production processes can optimize workflow efficiency and minimize bottlenecks. By incorporating leak testing stations directly into assembly lines or production cells, you can perform testing in situ, eliminating the need for additional handling and transportation of components.
Continuous Monitoring and Feedback
Implementing continuous monitoring and feedback loops allows for proactive identification and correction of issues during the testing process. Real-time data analytics and feedback mechanisms enable quick adjustments to testing parameters, ensuring consistent and reliable results while minimizing the risk of defects or failures.
Regular Calibration and Maintenance
Regular calibration and maintenance of helium leak testing equipment are essential to ensure accurate and reliable performance over time. Schedule routine calibration checks and preventive maintenance tasks to keep equipment in optimal condition and identify any potential issues before they affect testing accuracy.
Also Read: Power of Shot Blasting Machines with Quality Spares Centre
Addressing Common Challenges
Despite the benefits of helium leak testing, businesses may encounter certain challenges in implementing and maintaining effective testing procedures. Here are some common challenges and strategies for overcoming them:
Complex Test Objects
Testing complex or irregularly shaped objects can present challenges in achieving uniform pressurization and accurate leak detection. To address this issue, consider using custom fixtures or adaptors to ensure proper sealing and pressurization of test objects. Additionally, optimizing test parameters and employing advanced detection techniques can improve sensitivity and reliability when testing intricate components.
Small Leak Detection
Detecting small leaks, especially in high-pressure or high-volume systems, can be challenging due to the low flow rates involved. To enhance sensitivity and accuracy, utilize helium leak detectors with high-resolution sensors and advanced signal processing capabilities. Implementing multi-stage testing procedures and incorporating complementary detection methods, such as sniffer probes or tracer gas injection, can also improve small leak detection efficiency.
Environmental Factors
Environmental conditions, such as temperature variations, humidity levels, and background gas interference, can impact the accuracy and consistency of helium leak testing results. To mitigate these effects, maintain stable testing environments with controlled temperature and humidity levels. Additionally, perform regular background gas checks and calibration adjustments to account for ambient conditions and minimize interference.
Training and Education
Effective helium leak testing requires skilled operators who understand the principles of leak detection and are proficient in using testing equipment. Invest in comprehensive training programs to ensure that personnel are adequately trained in proper testing procedures, equipment operation, and troubleshooting techniques. Regular refresher courses and proficiency assessments can help maintain operator competency and optimize testing outcomes.
Conclusion
In conclusion, understanding the effectiveness of your helium leak testing system is crucial for ensuring the integrity, reliability, and safety of your products and processes. By considering factors such as leak rate, test pressure, detection equipment sensitivity, and testing environment, businesses can optimize their helium leak testing procedures and achieve accurate and reliable results.
Also Read: What is the Mainly Off-Grid Solar System’s Application 2024