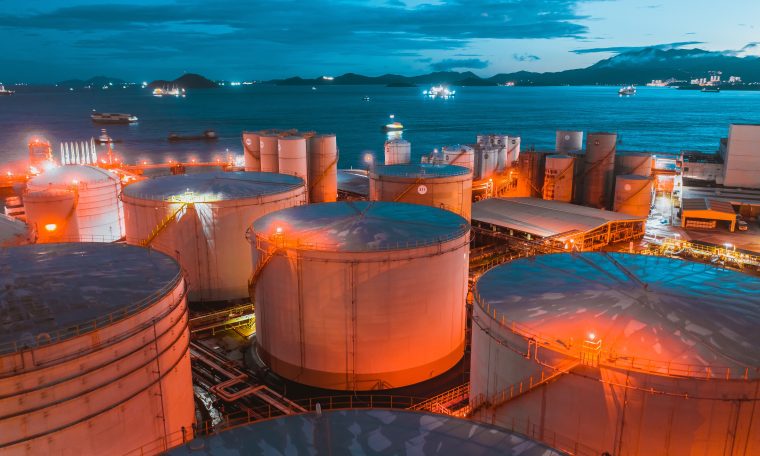
Storage tank calibration is fundamental in managing the storage of liquids, whether it be oil, chemicals, or water. The accuracy of storage tank data is paramount, as any inaccuracies can lead to significant issues. These include erroneous supply chain decisions and compromised safety protocols, especially when dealing with hazardous materials. Calibration ensures the integrity and accuracy of data, which is essential for maintaining operational efficiency and safety.
The Critical Role of Calibration in Measurement Accuracy
The process of storage tank calibration involves precise measurement and verification of the tanks’ capacities. This is crucial for ensuring accurate volume readings at various levels. By utilizing advanced technology and specific methodologies, this process helps in maintaining the supply chain’s integrity and operational safety.
storage tank calibration is more than just a procedural necessity. It is a key aspect of maintaining safety and efficiency in industries involved in liquid storage. It ensures that businesses operate smoothly and safely, complying with regulatory standards and avoiding measurement inaccuracies.
Accurate calibration is instrumental in ensuring the correct amount of liquids is stored, processed, and distributed. This aids in logistical efficiency and compliance with industry standards. Additionally, calibration is vital in safety management, preventing risks associated with overfilling or under-utilization of tanks. This not only safeguards the facility and its workers but also helps in minimizing environmental risks.
Tank calibration adjusts and validates the accuracy of a tank’s capacity or volume. Inaccuracies in tank measurements can result from different factors. They may include temperature variations, material expansion, or wear and tear over time. These errors can be subtle. But when compounded, they can lead to major discrepancies.
By conducting regular calibration of volume tanks, industries can catch and rectify errors. In petrochemicals or water treatment industries, having precise data is indispensable. In this blog, we will uncover various types of measurement errors in storage tanks and how to avoid them.
Types of Storage Tank Measurement Errors
Constant Error:
When there is a consistent data inaccuracy that persists over time – we call it constant error. It means that, regardless of the number of measurements, the error remains same. For example, if a storage tank shows a higher or lower volume reading, it is experiencing a constant error.
Random Error:
Random errors are unpredictable fluctuations in measurement readings. They can result from various factors, including sensor inaccuracies or external influences. Calibrating storage tanks helps identify and reduce random errors. This ensures more reliable and consistent volume measurements.
Systematic Error:
Systematic errors follow a consistent pattern. It often arises from specific conditions or equipment issues. Through systematic storage tank calibration, your can detect and correct these errors. Calibration helps prevent ongoing inaccuracies in volume measurements.
Gross Error:
Gross errors are significant mistakes that can affect measurement accuracy. These errors might result from human oversight or sensor malfunctions. Regular calibration serves as a preventive measure. It helps you to reduce the occurrence of gross errors and preserve data reliability.
Instrumental Error:
Instrumental errors originate from faults in the measuring instruments or sensors. These errors can lead to distorted readings. Routine maintenance and storage tank calibration address instrumental errors. It ensures that the measurement instruments are well-functioning.
Reading Error:
Reading errors occur when there are mistakes in interpreting the measurement readings. These errors may stem from human oversight or misalignment of measurement scales. Implementing proper training and adhering to standardized calibration procedures are a must. It helps reduce reading errors and maintain measurement precision.
Calibration Drift:
Calibration drift is the shift in the accuracy of measuring instruments over time. This phenomenon can introduce errors if not addressed without delay. Regular and systematic calibration can help you identify this mistake and ensure accuracy.
Environmental Error:
Environmental factors can introduce errors in storage tank measurements. They may include temperature changes or external vibrations. These errors are often unpredictable. They highlight the importance of regular calibration of storage tanks. This helps to mitigate the impact of environmental conditions on measurement accuracy.
How Do You Ensure Accuracy
Regular Calibration:
Ensure accuracy by conducting regular calibration of storage tanks. This involves adjusting and validating the tank’s measurement system. Regular calibration minimizes errors and maintains precise measurements.
Temperature Monitoring:
Keep tabs on temperature variations to prevent inaccuracies. Temperature changes can impact the volume readings. Use measures to track and adjust for these variations. It will help you enhance the accuracy of storage tank measurements.
Sensor Maintenance:
Maintain the sensors used for measuring tank levels. Regular checks and maintenance activities help prevent sensor inaccuracies. Ensuring the proper functioning of sensors contributes to reliable and error-free volume measurements.
Environmental Controls:
Introduce controls to reduce the impact of external factors. Protect storage tanks from vibrations or other environmental influences that can distort measurements. Creating a stable environment around the tank supports accurate volume readings.
Periodic Inspection:
It is essential to conduct regular inspections of storage tank components. This process involves a thorough examination for signs of wear and tear, which can occur over time due to constant use and exposure to various elements. Additionally, inspectors should look for sediment buildup, a common issue in storage tanks that can significantly affect the accuracy of measurements if left unchecked.
These inspections are not just about identifying visible issues; they also play a crucial role in maintaining the overall integrity and functionality of the storage tanks. Sediment accumulation, for instance, can lead to incorrect readings and potentially cause operational inefficiencies or safety hazards. By detecting these problems early, necessary maintenance or repairs can be undertaken to ensure that the tanks continue to operate accurately and efficiently.
Training and Procedures:
Provide adequate training for personnel involved in tank measurements. Ensure that you follow standardized procedures for storage tank calibration with care. Proper training and abiding by protocols help reduce human errors and enhance accuracy.
Quality Control Measures:
Implement quality control protocols to identify and rectify errors promptly. Consistently monitoring the calibration process, assessing sensor functionality, and evaluating environmental factors is essential. Such proactive quality control steps are crucial for maintaining continuous accuracy in storage tank measurements.
Data Validation:
Regular data validation is crucial in maintaining the accuracy of storage tank measurements. By including validation checks, any anomalies or inconsistencies in the readings can be identified and addressed promptly. This practice ensures the reliability and trustworthiness of measurement data. In various industries, the accuracy of storage tank measurements is of paramount importance. Frequent calibration is key to correcting potential errors and maintaining precision in measurements. Addressing factors like temperature variations and sensor malfunctions through regular calibration is essential for ensuring data accuracy. Therefore, consistent calibration of storage tanks is vital to ensure the measurements obtained are accurate and dependable.