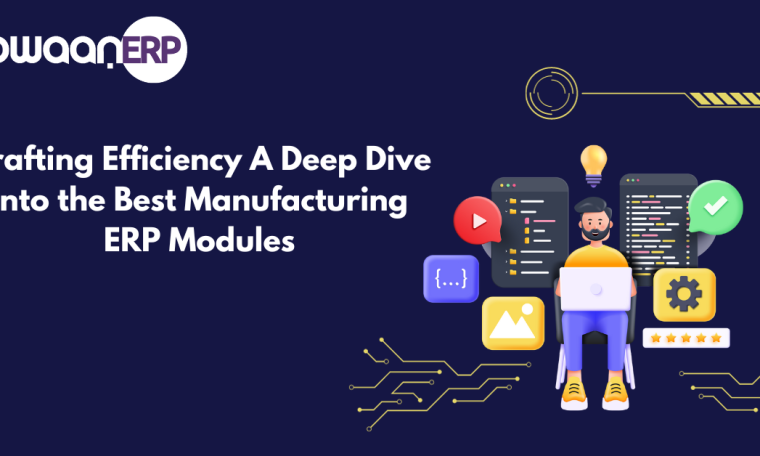
The evolving manufacturing landscape requires the integration of Enterprise Resource Planning (ERP) systems. The best erp system in saudi arabia comprises modules that optimize and streamline various operational aspects. Explore the Key ERP modules to Buy the best ERP system in Saudi Arabia revolutionizing manufacturing efficiency.The evolving manufacturing landscape requires the integration of Enterprise Resource Planning (ERP) systems for Crafting Efficiency with manufacturing modules.
Inventory Management Module
This module ensures optimal inventory levels by tracking raw materials, finished goods, and work-in-progress inventory for Crafting Efficiency. Real-time inventory monitoring helps make informed decisions to prevent stockouts and minimize excess stock. This leads to cost savings and efficient production planning.
The Inventory Management Module is a crucial component in tracking, controlling, and optimizing inventory by efficiently managing stocks, streamlining procurement, and maintaining optimal inventory levels.
Key Functions:
Inventory Tracking:
Inventory tracking is a fundamental process for monitoring and managing the movement of stocked goods. The real-time insights into the quantity, location, and status of inventory items throughout the supply chain aid in informed decision-making. Keeping track of stocks helps in avoiding stockouts or overstock situations.
Supplier Management:
This module manages vendor relationships, tracks deliveries, and ensures seamless communication for timely stock replenishment.
Inventory Valuation:
Calculates different inventory methods for accurate financial reporting.
Demand Forecasting:
Historical data and trends assist inventory planning and reduce the risk of overstocking or shortages.
Order Management:
The inventory management module facilitates order processing for the timely fulfillment of orders. It reduces lead times for customer satisfaction.
Inventory Optimization:
This module uses real-time analytics to optimize inventory levels and reduce holding costs.
Production Planning and Control
This module assists in planning, scheduling, and controlling manufacturing processes to optimize production schedules, resource allocation, and capacity planning. It reduces lead times and enhances resource utilization for Crafting Efficiency.
Production Planning and Control (PPC) is a critical function to ensure efficient and effective utilization of resources. This helps in meeting production targets and delivering high-quality products.
Key Aspects:
Demand Forecasting: It analyzes historical data and market trends for better production planning.
Capacity Planning: It assesses available resources to align production capacity with demand.
Scheduling: Drafts schedules for production activities and resource allocation for each task.
Materials Requirement Planning (MRP): Estimates raw materials to prevent shortages or excess inventory.
Optimizing Workflow: Offers smooth and efficient workflow by reducing lead times.
Quality Control: Implements measures to maintain product quality to ensure adherence to standards.
Performance Monitoring: Tracks and analyzes production performance metrics to improve.
Quality Management
As the name suggests, this module oversees quality control measures to manage quality inspections, ensure compliance with standards, and identify areas for process improvement. The Benefits of ERP software in Saudi Arabia include higher-quality outputs and customer satisfaction.
Quality Standards
Establishment: Defining quality benchmarks for products or services to meet the highest standards.
Quality Planning:
Developing strategy to meet customer requirements.
Quality Assurance:
Implementing processes to establish quality standards for service delivery.
Quality Control:
Conducting inspections to rectify issues before products reach customers.
Continuous Improvement:
We are using Six Sigma to enhance processes, products, or services.
Customer Feedback and Satisfaction:
We collect and analyze customer feedback to ensure customer satisfaction.
Training and Employee Involvement:
We are providing training and fostering a culture of quality to maintain high-quality standards.
Supply Chain Management
This module streamlines the supply chain to enhance visibility across the supply chain. Case studies on the best ERP system implementations in Saudi Arabia show that an ERP system is mandatory for managing vendor relationships, procurement processes, and logistics to minimize delay. This module optimizes supplier collaboration for an efficient supply network for Crafting Efficiency.
Sourcing and Procurement: Identifies suppliers, negotiates contracts, and sources raw materials.
Inventory Management: Manages inventory levels to minimize carrying costs and obsolescence.
Logistics and Distribution: Planning and coordinating transportation to reach customers efficiently.
Supplier Relationship Management: Cultivating solid relationships with suppliers for mutual benefit.
Demand Planning: Forecasting customer demand to meet fluctuating demand patterns.
Risk Management: Identifies potential risks to mitigate them.
Performance Measurement: Monitoring supply chain metrics to identify areas for improvement.
Benefits:
Cost Efficiency: Reduces waste to save costs across the supply chain.
Improved Collaboration: Enhances communication and collaboration among stakeholders.
Enhanced Responsiveness: Adapts to changes in demand to ensure agility in the supply chain.
Customer Satisfaction: Ensures product availability for customer satisfaction.
Shop Floor Control
Real-time insights into manufacturing activities optimize production efficiency and reduce downtime. Better shop floor management is possible with machine utilization and labor resources for Crafting Efficiency.
Production Monitoring:
Tracks all the production activities like machine operations, assembly lines, and workstations.
Work Order Management:
Prioritizes work orders for timely execution.
Resource Allocation:
Allocates and manages resources to optimize production processes.
Quality Assurance:
Ensure product quality throughout the manufacturing process with different processes.
Financial Management
ERP systems integrate financial data to manage accounting, budgeting, cost tracking, and financial reporting. This is vital for better financial decision-making and cost control.
Financial Management is integral for decision-making, transparency, and accountability. Managing finances is a critical task that offers financial health, supports growth initiatives, and helps to make informed strategic decisions.
Budgeting:
Create budgets for various departments and monitor expenditures.
Financial Reporting:
Generates financial statements according to the organization’s economic performance.
Risk Management:
Mitigating financial risks for profitability and stability.
Cash Flow Management:
Monitors cash inflows to meet obligations.
Business Intelligence and Analytics:
This module offers insights into production performance, trends, and forecasts to enable proactive strategies that empower decision-makers with actionable information. The aggressive strategy drives improvements across manufacturing operations.
Data Collection: Gathering and compiling data from internal and external sources.
Processing and Cleansing: Cleaning and transforming raw data to ensure data accuracy and consistency.
Data Analysis: Utilizing analytical tools to extract valuable insights.
Reporting and Visualization: Creating visual representations to present analyzed data.
Conclusion
ERP modules pave the way for sustained growth by empowering manufacturing enterprises to streamline processes. They can optimize resources and drive efficiency to ensure competitiveness within the manufacturing landscape.These capabilities help navigate market complexities by responding swiftly to changing demand. It is a must-have tool for success in today’s dynamic business environment.